Teflon®
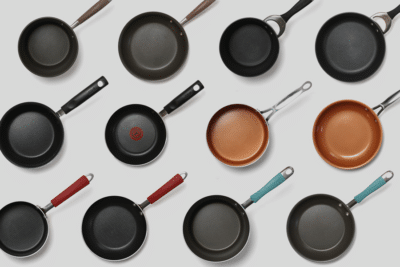
Fluorous media are highly non-polar and notoriously poor solvents. The “fluorous nature” of fluorocarbons refers to their macroscopic phase behavior. Compared to hydrocarbon analogs, fluorocarbons are more rigid and have a larger cross-sectional area, and they pack less densely and display much smaller van der Waals interaction energy per molecular contact area. As a dimensionally stable fluorous matrix, perfluoropolymers are receiving increased attention in both the scientific community and industry. The most well-known property shared by perfluoropolymers is their extraordinary thermal and chemical stability due to the strong carbonfluorine and carbon-carbon bonds. [Zhang, H. (2014). Teflon AF Composite Materials in Membrane Separation and Molecular Recognition in Fluorous Media (Doctoral dissertation, University of Pittsburgh)].
Teflon® is a brand name for a man-made chemical copolymers of tetrafluoroethylene (PTFE) and 2,2-bis(trifluoromethyl)-4,5-difluoro-1,3-dioxole used as membrane materials. The primary chemical in Teflon, polytetrafluoroethylene (PTFE), has a high melting point (327 ºC), making it ideal for cooking applications. However, when heated to temperatures above 350 ºC (662 ºF), PTFE begins to degrade, releasing fine particles and a variety of gaseous compounds that can cause damage to the lungs when inhaled. It has been in commercial use since the 1940s. It has a wide variety of uses because it is extremely stable (it doesn’t react with other chemicals) and can provide an almost frictionless surface.
Filled PTFE is obtained by blending virgin PTFE with fillers, such as carbon, glass fibre, graphite, ceramic, nickel, stainless steel, bronze, MoS2, polyimide and others.
Filled PTFE enhances several PTFE properties required by specific industrial applications, such as compressive resistance, heat conductivity and reduced creep (cold flow).
Other registered trademarks derived from fluoropolymers from the same manufacturer include (with very closed chemical compositions):
- Teflon AF Among commercially available perfluoropolymers, the Teflon AF family is an unusual class of amorphous glassy copolymers with a high fractional free volume (FFV). Teflon AFs are copolymers of tetrafluoroethylene (TFE) and 2,2-bistrifluoromethyl-4,5-difluoro-1,3 dioxole (BDD). Two types of Teflon AF, produced by DuPont, are now available in market:Teflon AF 2400 (TFE: 13 mol%; BDD: 87 mol%) and Teflon AF 1600 (TFE: 35 mol%; BDD: 65 mol%) [Zhang, H. (2014). Teflon AF Composite Materials in Membrane Separation and Molecular Recognition in Fluorous Media (Doctoral dissertation, University of Pittsburgh)].
- Teflon-PFA (perfluoroalkoxy (PFA)) which is a transluent copolymer with chemical properties similar to the PTFE, although having a lower fusion point at around 250 °C.
- Teflon-FEP (fluoroéthylène propylène (FEP)) which is a copolymer composed from hexafluoropropylene and tétrafluoroéthylène. These fusion point is approximately of 205° C, rendering this materila highly unsafe for cooking
- Tefzel (Ethylene tetrafluoroethylene (ETFE)). ETFE has a relatively high melting temperature, excellent chemical, electrical and high-energy radiation resistance properties. When burned, ETFE releases hydrofluoric acid (HF). HF is extremely corrosive and toxic, and so appropriate caution must be exercised.
- Teflon FFR (Fluoroplastic Foam Resin): Perfluoroethylene propylene copolymer. Fluoroplastic foam resin is an alternative to expanded PTFE tape with characteristics that ease the manufacturing process. Fluoroplastic foaming resins are innovative technology which reduces the dielectric constant, whilst still providing fast data transmission with minimal distortion. Fluoroplastic foaming resins are therfore particularly adapted for copper wire insulationand allows manufacturers to produce lighter and smaller wires.
- Tefzel is the registered brand name of Ethylene tetrafluoroethylene (ETFE) which is a fluorine-based plastic. It was designed to have high corrosion resistance and strength over a wide temperature range. ETFE has a relatively high melting temperature, excellent chemical, electrical and high-energy radiation resistance properties. When burned, ETFE releases hydrofluoric acid (HF). HF is extremely corrosive and toxic, and so appropriate caution must be exercised. ETFE resins are resistant to ultraviolet light. An accelerated weathering test (comparable to 30 years’ exposure) produced almost no signs of film deterioration.Therefore ETFE applications include outdoor covering.
Perfluorooctanoic acid (PFOA), also known as C8, is another man-made chemical. It is used in the process of making Teflon and similar chemicals (known as fluorotelomers). PTFO is a adhesive element necessary to stick the Teflon coating with the middle layer material.
PFOA has the potential to be a health concern because it can stay in the environment and in the human body for long periods of time. Studies have found that it is present worldwide at very low levels in just about everyone’s blood. Furthermore, it is very worriying to notice that the fusion temperature of PFOA is approximately 50° C, temperature that is reached after few seconds of cooking.
Mechanical Properties [https://www.chemours.com/Teflon_Industrial/en_US/tech_info/techinfo_compare.html]
Property | ASTM Standard | Unit | PTFE | FEP | PFA | ETFE |
Specific Gravity | D792 | — | 2.15 | 2.15 | 2.15 | 1.76 |
Tensile Strength | D1457 D1708 D638 | MPa (psi) | 21-34 (3,000-5,000) | 23 (3,400) | 25 (3,600) | 40-46 (5,800-6,700) |
Elongation | D1457 D1708 D638 | % | 300-500 | 325 | 300 | 150-300 |
Flexural Modulus | D790 | MPa (psi) | 496 (72,000) | 586 (85,000) | 586 (85,000) | 1,172 (170,000) |
Folding Endurance | D2176 | (MIT) cycles | >106 | 5-80 x 103 | 10-500 x 103 | 10-27 x 103 |
Impact Strength | D256 | J/m (ft·lb/in) | 189 (3.5) | No Break | No Break | No Break |
Hardness | D2240 | Shore D pencil | 50-65 HB |
56 HB | 60 | 72 |
Coefficient of Friction, Dynamic | D1894 | — | 0.05-0.10 | 0.08-0.3 | — | 0.3-0.4 |
Thermal Properties [https://www.chemours.com/Teflon_Industrial/en_US/tech_info/techinfo_compare.html]
Property | ASTM Standard | Unit | PTFE | FEP | PFA | ETFE |
Melting Point | D3418 | °C (°F) | 327 (621) | 260 (500) | 306 (582) | 267 (512) |
Cure Temperature | — | °C (°F) | 379-429 (715-805) | 360-385 (680-725) | 379-399 (715-750) | 302-323 (575-615) |
Flame Rating* | UL94 | — | V0 | V0 | V0 | V0 |
Limiting Oxygen Index | D2863 | % | >95 | >95 | >95 | 30-36 |
Heat of Combustion | D240 | MJ/kg (Btu/lb) | 5.1 (2,200) | 5.1 (2,200) | 5.3 (2,300) | 13.7 (5,900) |
* Statements regarding behavior in a flame situation are not intended to reflect hazards presented by this or any other material when under actual fire conditions.
Chemical Properties [https://www.chemours.com/Teflon_Industrial/en_US/tech_info/techinfo_compare.html]
Property | ASTM Standard | Unit | PTFE | FEP | PFA | ETFE |
Chemical/Solvent Resistance | D543 | — | Excellent | Excellent | Excellent | Excellent |
Water Absorption, 24 h | D570 | % | <0.01 | <0.01 | <0.03 | <0.03 |
Salt Spray Resistance (1) -on aluminum -on steel | B-117 | Hours Hours | 744+ 192 | 744+ — | 1000 — | 1000 — |
Detergent Resistance (2) -on aluminum -on grit-blasted aluminum -on grit-blasted steel | — | Hours Hours Hours | 264 624 24 | 744 600 480 | — — — | — — — |
Weather Resistance | Florida Exposure | Years Unaffected | 20 | 20 | 10 | 15 |
Notes:
1. Salt Spray Resistance: 5% NaCl at 35°C/95°F, hours to failure
2. Detergent Resistance: hours to failure
Electrical Properties [https://www.chemours.com/Teflon_Industrial/en_US/tech_info/techinfo_compare.html]
Property | ASTM Standard | Unit | PTFE | FEP | PFA | ETFE |
Dielectric Constant | D150 | 1 MHz | 2.1 | 2.1 | 2.1 | 2.6 |
Dielectic Strength* | D149 | V/µm | 18 | 53 | 80 | 79 |
Dissipation Factor | D150 | 1 MHz | <0.0001 | 0.0006 | 0.0001 | 0.007 |
Arc Resistance | D495 | sec | >300 | 300 | >180 | 122 |
Volume Resistivity | D257 | ohm·cm | >1018 | >1018 | >1018 | >1017 |
Surface Resistivity | D257 | ohm/sq | >1018 | >1016 | >1017 | >1015 |
* Dielectric Strength: 100 micrometers film
More informations about Teflon patents: http://www.fluoride-history.de/p-teflon.htm, http://www.fluoride-history.de/index.htm]
You can also buy Teflon materials to perform your own tests:
[An Introduction to Chemours™ Fluoropolymers, Teflon™ PTFE, PFA, FEP Fluoropolymers, Tefzel™ ETFE, Fluoropolymer, Zonyl™ PTFE Fluoroadditive, Chemours, 2018] [https://www.chemours.com/Teflon_Industrial/en_US/products/product_by_name/teflon_af/grades.html] [https://www.alfa-chemicals.co.uk/products/teflon-ffr] [https://theintercept.com/series/the-teflon-toxin/]
Several dangerous chemicals have been replaced by what environmentalists call “regrettable substitutions,” molecules that are often just slightly tweaked versions of the originals and pose similar problems.Sharon Kelly
Ceramic
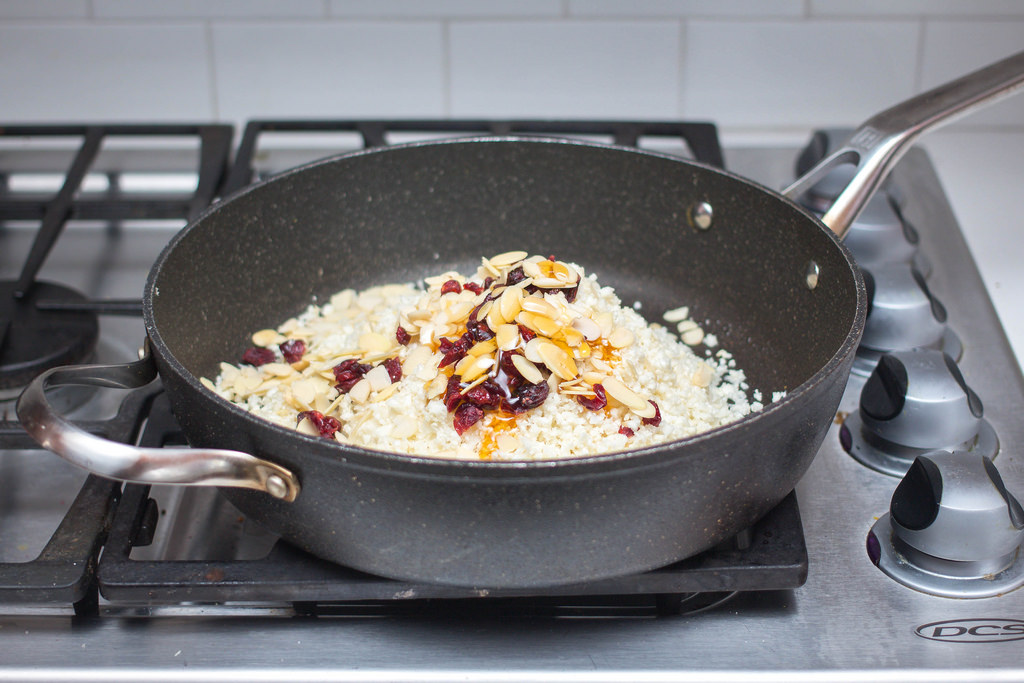
Ceramics can be classified into three distinct material categories
and each one of these classes can be developed into unique material
properties because ceramics tend to be crystalline:
• Oxides: alumina, beryllia, ceria, zirconia
• Non-oxides: carbide, boride, nitride, silicide
• Composite materials: particulate reinforced, fiber reinforced, combinations of oxides and nonoxides.
Ceramic technically means « clay that has been fire hardened ». So when we talk of ceramic coated cookware, we are talking about some sort of metal (usually hard anodized aluminum) that has been coated with a layer of ceramic. Ceramic non-stick coatings are typically made from inorganic minerals, primarily silicon and oxygen. Inorganic means not containing any carbon
Most ceramic non-stick coatings are applied using a Sol-gel process. Sol-Gel is a process that converts the inorganic liquid Solution into a Gel that can be applied to any metallic substance. Sol-gel coatings are applied either by spray or by dipping the item in the mineral gel which is then hardened by a high heat firing process known as curing.
First example of ceramic non-sick coating composition : A series of new non-stick ceramic coating materials prepared from organic-inorganic hybrid materials, including silica sol, MTMS, FAS and PDMS (Polydimethylsiloxane) using the sol-gel process. The hybrid materials have good mechanical properties and are fashioned into a main ceramic network and good non-stick properties from organic non-stick compounds.
Second example of ceramic non-stick coating : he novel coating includes a SiO2 ceramic matrix that includes the condensation product of hydrolyzed alkoxysilane and a colloidal silica sol. A series of new abrasion resistant and high hardness non-stick coating materials have been developed with ceramic matrix and organic compounds by sol-gel process. This non-stick material has two main component of silicon dioxide. One is silica sol which is pure SiO2, another is an organoalkoxysilane which is an organic-inorganic hybrid material.
Pure ceramic coating
Pure ceramic cookwares may be unsafe due to the natural composition of ceramic. Conventional ceramics are very heterogeneous physical and chemical mixtures of oxide compounds and glasses, containing large impurities. Similarly to clay, pure (conventional) ceramics often contain high amount of aluminum and silica.
Clay cookware
Natural clay cookware may be unsafe because clay contains high amount of Aluminum and very large amounts of silicon. Please find an interesting article on clay composition following this link https://ireadlabelsforyou.com/clay-cookware-safe-or-toxic/
Granite cookware
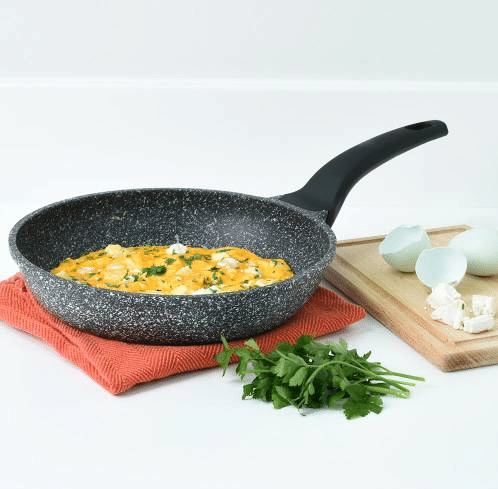
Granite cookware is a material used in frying pans. Today granite cookware and granite pans are made with a stainless steel core and topped with a glass coating. Most granite cookware has a porcelain enamel fused at 2,000 F. This creates a non-stick glass surface that’s non-porous and inert. Coating may also include PFOA and PTFE on the pans. These are the same chemicals used in Teflon
Soapstone (steatite) cookware
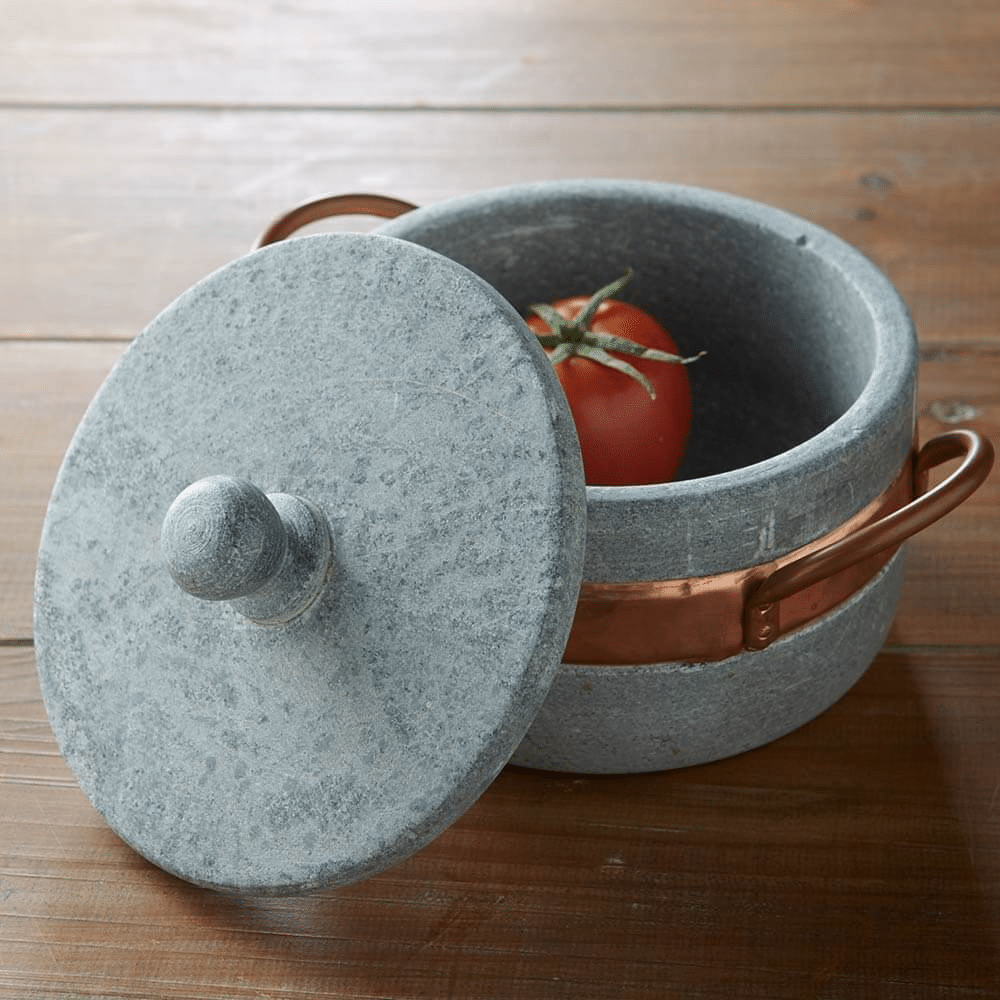
By mass, “pure” steatite is roughly 63.37% silica, 31.88% magnesia, and 4.74% water. It commonly contains minor quantities of other oxides such as CaO or Al2O3.They most probably contain asbestos and large amount of chlorite, iron-chromium oxides
Copper cookware
Copper is the best heat conductor of any material used to make cookware. It heats rapidly and evenly and cools down as soon as it’s removed from the heat, giving you maximum control over the application of heat. How quickly a pan responds to a change in cooking temperature is referred to as “responsiveness” and can be a significant factor in choosing what pan will deliver the best results for different jobs. Since copper is the most highly responsive type of cookware, it is highly prized by professional chefs the world over. The best-quality copper pans are made of a heavy gauge, 1/16 to 1/8 inch thick.
However, copper cannot be used alone for most cookware applications because it “reacts” with the natural minerals and acids of many foods. That means it can add a yellow tint and metallic taste to many foods. For that reason most copper cookware must be lined with a nonreactive metal such as tin or stainless steel to create a safe barrier between the copper and its contents. Traditionally, tin is the material used to line copper cookware because it is responsive and nonreactive.
Aluminium cookware
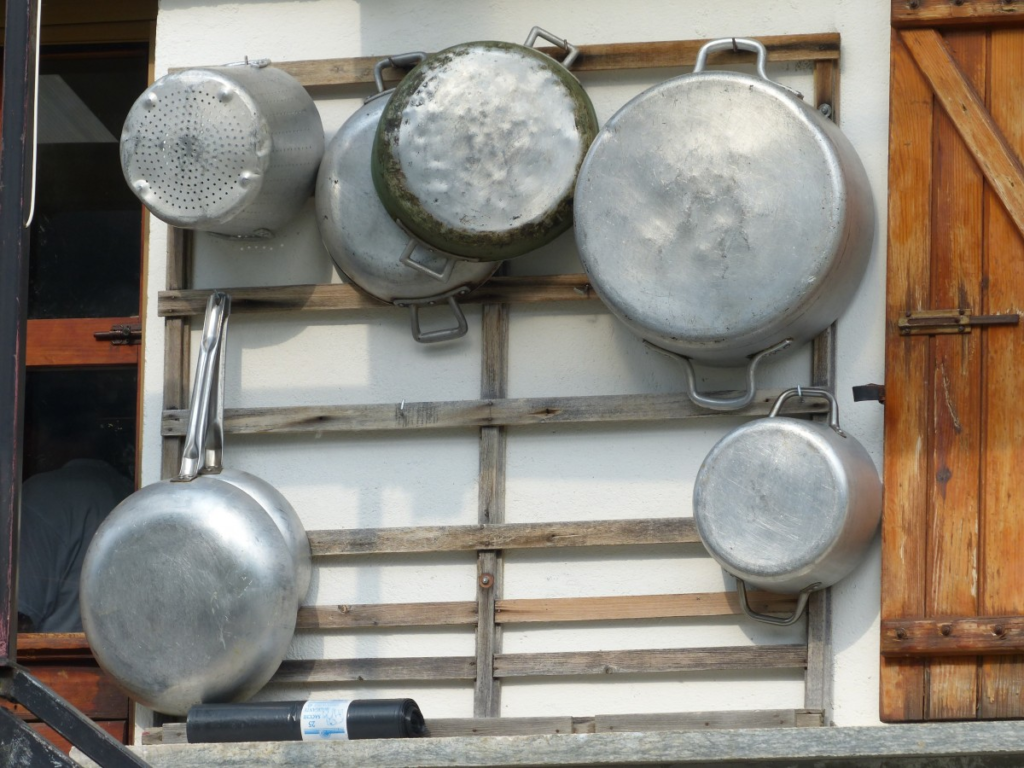
Pure aluminum is second only to copper in heat conductivity. It is inexpensive, and when strengthened (usually by adding magnesium, copper or other metals) it makes wonderfully light and responsive cookware on its own. But as you may have guessed, natural aluminum will react with certain acidic foods, imparting a metallic taste and dull gray tint. To address this shortcoming, the best pieces are either lined with a nonstick coating, clad with stainless steel, or undergo anodization (a process that significantly hardens the surface and gives it a very dark grey color). In fact, more and more manufacturers are anodizing pieces that will also have nonstick or stainless interiors because it is attractive, more durable and easier to clean
Stainless steel cookware
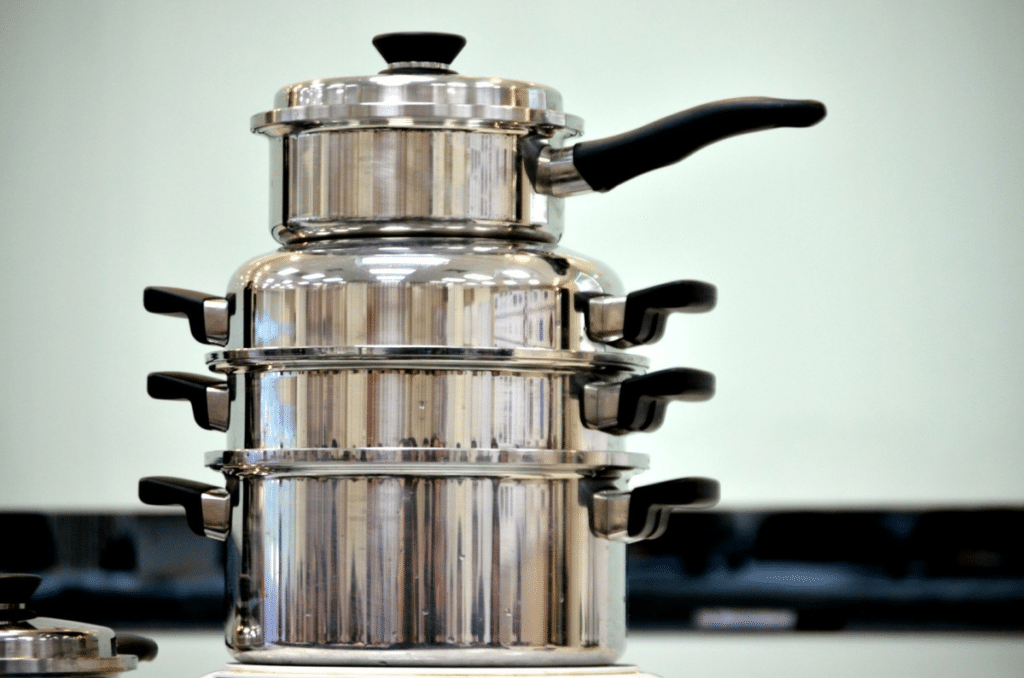
Stainless steel cookware is made from a metal alloy consisting of mostly iron and chromium along with differing percentages of molybdenum, nickel, titanium, copper and vanadium. But even stainless steel allows other metals to leach into the foods. The principal elements in stainless that have negative effects on our health are iron, chromium and nickel.
Depending on the stainless steel alloy, Molybdenum may also be integrated. For example: the AISI 316 alloy made of FeCr18Ni10Mo3
[https://www.sigmaaldrich.com/catalog/search?term=polytetrafluoroethylene&interface=All&N=0&mode=partialmax&lang=fr®ion=FR&focus=product
Carbon steel
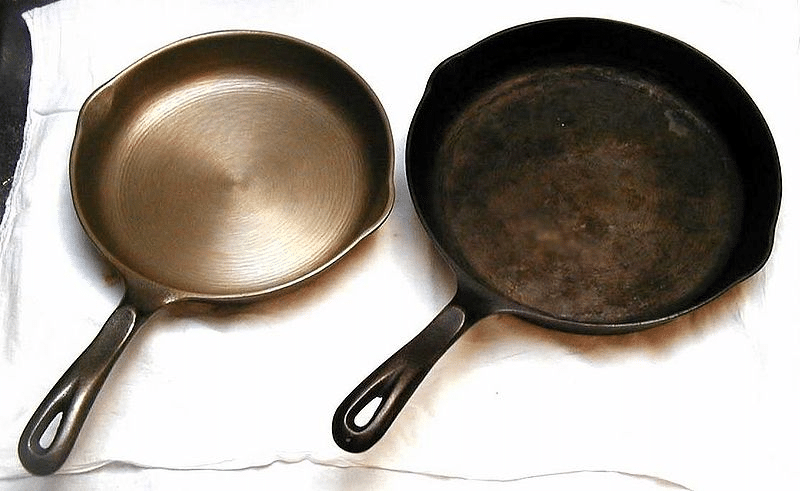
Carbon steel follows aluminum in heat conductivity. Although inexpensive and very durable, raw carbon steel is relegated to specialty pan use, mainly as a skillet or wok. One reason for this is carbon steel will rust if not seasoned (oiled) properly. The good news is that if it is seasoned properly it will develop a naturally nonstick interior (very much like cast iron), and experienced cooks will find them to be highly versatile. The pans are somewhat heavy and a little slow to heat, they can react a bit with very acidic foods and maybe are not the best all-rounders. But they can achieve a higher temperature than other pans and hold the heat well, which makes them ideal for certain high heat techniques
Carbon steel cookwares release large amount of iron in the foods, making them unsafe for people with hemochromaturia but particularly advised for ferrous anemia patients or vegans.
Cast iron
Cast Iron is a poor conductor of heat; which means it’s slow to heat up and slow to cool down. But this self-regulating nature makes cast iron a preferred material for dutch ovens, fry pans, griddles and grill pans. These pieces are exceedingly durable and resist warping, denting and chipping. Cast iron cookware is available in its natural state or enamel coated and both cook similarly but there are other notable differences. Natural cast iron costs substantially less, but it requires the user to apply a “seasoning” coat to protect it from rust.
Cast iron cookwares release large amount of iron in te foods, making them unsafe for people with hemochromaturia but particularly advised for ferrous anemia patients or vegans.
Enamelled cast iron
Enameled Cast Iron pieces are maintenance free- easy to clean, completely nonreactive and boast beautifully colored glazes… benefits that are, of course, reflected in the higher cost
Glazed materials or painting used to coat the cast iron can be very dangerous since they usually contain heavy metals such as lead and cadmium
Glass
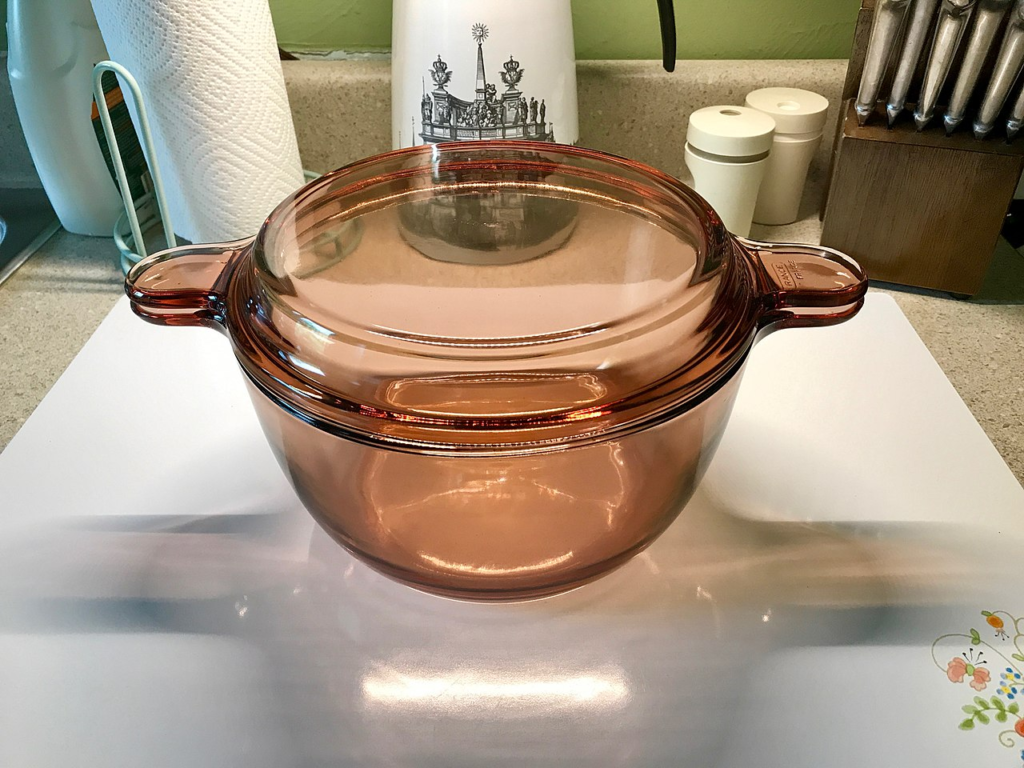
Made of resistant Borosylicate material, which is relatively safe.
However when submitted to important temperature changes, it may break and may release hot food which is very dangerous.
Porcelain
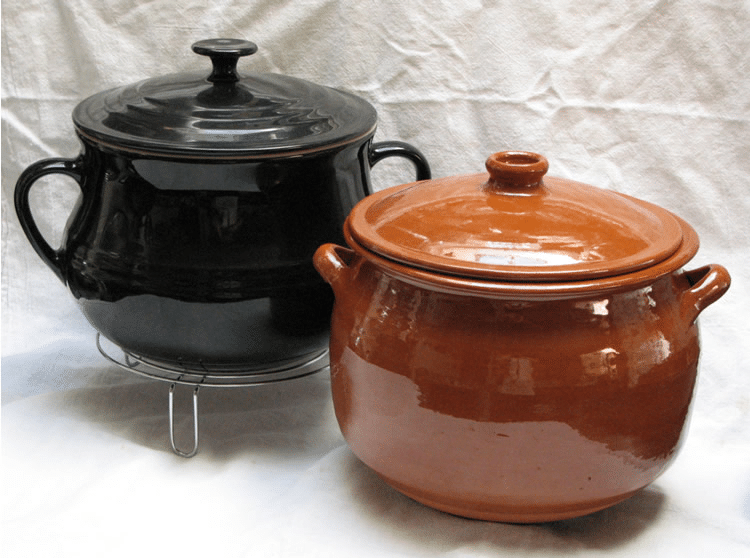
Porcelain is a type of ceramic that is composed mostly of a white clay called kaolin with the addition of feldspars, quartz, steatite and other substances. The whole compound is cooked at 1300-1400 degrees. As well as clay and glass ceramics, porcelain may be glazed or not.
Porcelain are typically not used with sudden change in temperature, as it may crack. However, enamel porcelain may permit to cook in porcelain cookware by adding conducting materials in the porcelain composition or in the coating. For a very vast majority of them, these coatings are dangerous. Enameled cookware are very dangerous : they may contain lead and cadmium.